Contact our friendly team for more information on our full range of buildings and how to start the process of hiring or buying a modular building for your business. Our expert team is always available to give advice, guidance or support.
Published: 6 June 2019 in Building Types
How Have Modular Buildings Improved Over The Past Decade?
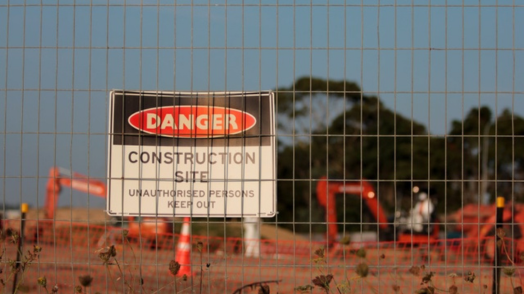
Off-site construction as a technique is a relatively modern approach to the construction sector. Modular buildings in particular are an even more recent concept in comparison to the world’s extensive construction history, but the distinct advantages of off-site methods have resulted in its popularity increasing as it develops year on year.
During a time in which the implementation of social infrastructure needs to be quick enough to meet the demands of an increasing population, many more businesses and local councils are turning to modular buildings as a viable and cost-effective option to offer this much needed space. In light of this rich history of modular buildings, this blog we will take a look at how this type of building and the techniques deployed to produce them have improved from when they were first manufactured.
From humble origins to the tallest tower
The inspiration for this blog stems directly from the news of a recent development of a hotel in New York. The creation of a 360-foot tower, produced through modular building techniques, will see the tallest modular hotel in the world erected in the city. As one of the latest additions to the Marriott International brand, the hotel is set to be constructed over 90 days and will contain 168 rooms over 26 storeys, in addition to a rooftop bar. Named the AC Hotel New York NoMad, the hotel is set to open in 2020. A 360-foot hotel is a stark representation of how far off-site construction has come!
These developments become particularly evident in comparison to how off-site construction began. One of the earliest recordings of prefabricated homes for example traces back to London carpenter Henry Manning. He endeavoured in 1837 to construct a house for his son who was emigrating to Australia. In manufacturing the components for it, the house was shipped and assembled down under. The success of the house saw a vast increase in demand for such prefabricated homes and several hundred were transported to Australia in 1853 alone. As the decades passed, off-site construction was used to construct temporary housing following World War II and more recently has been used to support NHS infrastructure across the country. So it’s as clear as ever how far off-site construction has come.
Today’s modular buildings by Springfield
The off-site techniques we employ here at Springfield are representative of the developments of this construction method over the past few decades. Although we do not produce homes or hotels, we have over 40 years of experience in the industry in providing businesses, schools and healthcare companies with a range of bespoke buildings. We offer a range of building types, from modular and portable to prefabricated and jackleg – ensuring we can meet the exact requirements of every single client.
All of our buildings are produced in our ISO-approved workshop in St Helens, where our expert team can inspect and perfect the smallest of details of each project. The controlled environment of the workshop ensures we are not affected by the weather, so the time it takes to complete a build is significantly shortened. It also means the team can recycle more of the products we use. Your building can therefore be delivered at fantastic speed and at extremely competitive cost, to be assembled on site in a matter of days.
These distinctive benefits of off-site construction are shown in the developments within the industry. If you would like to find out more about the modular buildings we offer then visit our website, or contact our team by calling 01744 851958.